تشخیص عمر باقی مانده بلبرینگ
زمانی که بلبرینگ یا بلبرینگ ها دیگر برای هدف مورد نظر خود مناسب نباشند، پایان عمر بلبرینگ فرا میرسد یا زمانی که چرخش متوقف میشود. در کاتالوگهای تولیدکنندگان بلبرینگ و بیشتر کتابهای طراحی مهندسی، پدیدهای که طول عمر و قابلیت اطمینان یاتاقان را محدود میکند، خستگی عنصر غلتشی نامیده میشود. این پدیده برای بیش از 120 سال از دهه 1890 با کار پیشگام ریچارد استریبک در آلمان و همچنین در اوایل قرن بیستم با جان گودمن در بریتانیای کبیر و آروید پالمگرن در سوئد مورد مطالعه قرار گرفته است.
مشارکت پالمگرن احتمالاً مهمترین کمک به فناوری بلبرینگ عناصر نورد بود. در سال 1924 او پایه و اساس محاسبه عمر بلبرینگ را فراهم کرد. او بیان کرد که تحمل زندگی قطعی نیست، بلکه توزیعی است. منظور او این بود که هیچ دو یاتاقان در یک گروه تحت شرایط یکسان کار نمیکنند یا در یک زمان خراب نمیشوند.
برای حدود 90 تا 95 درصد کاربردهای طراحی ماشین، معادلات و توصیههای موجود در کاتالوگ سازندگان بلبرینگ، طراحی ایمن و قابل اعتماد را فراهم میکنند. معمولاً 5 تا 10 درصد باقی مانده از برنامه ها نیاز به دانش و تجزیه و تحلیل تخصصی دارند تا دچار مشکل نشوند.
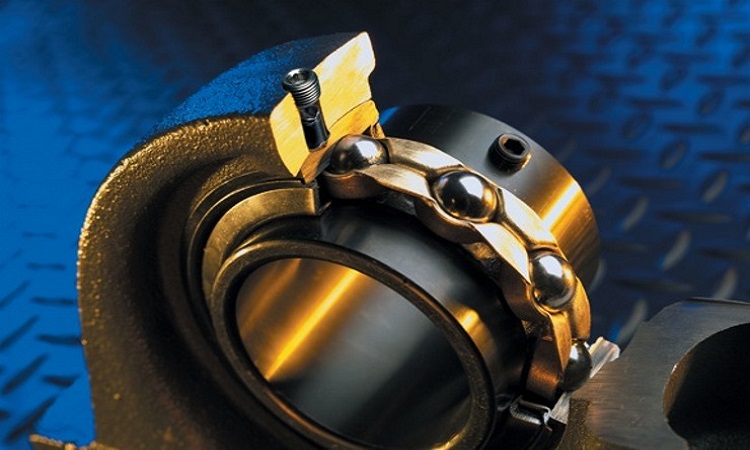
حالت های شکست
حالت شکست نهایی که عمر یاتاقان را محدود می کند، خستگی عنصر غلتشی یاتاقان یا المان غلتشی است. خستگی عنصر غلتشی بسیار متغیر است، اما بسته به نوع فولاد، پردازش فولاد، عملیات حرارتی، ساخت و نوع بلبرینگ، روان کننده مورد استفاده و شرایط عملیاتی، از نظر آماری قابل پیش بینی است.
شکست خود را به صورت ریزش نشان می دهد که به عرض مسیر دویدن و عمق حداکثر تنش برشی زیر سطح تماس محدود می شود. اسپال می تواند منشا سطحی یا زیرسطحی داشته باشد. یک ریزش که از سطح منشا می گیرد معمولاً به عنوان یک ترک در یک نقص سطح یا در یک فرورفتگی باقی مانده که در شبکه ترک منتشر می شود و یک ریزش ایجاد می کند شروع می شود. ترکی که از یک افزایشدهنده تنش شروع میشود، مانند یک گنجایش سخت در زیر مسیر دویدن در ناحیه حداکثر تنش برشی، همچنین در یک شبکه ترک منتشر میشود تا شکاف ایجاد کند.
خرابی های خستگی که در زیر سطح تماس ایجاد می شوند به عنوان خستگی عناصر غلتشی کلاسیک نامیده می شوند. شکست ناشی از خستگی کلاسیک عنصر غلتشی مشابه مرگ ناشی از پیری در انسان است. با این حال، اکثر بلبرینگ ها به دلایل دیگری از سرویس خارج می شوند.
اگر یاتاقان بیش از حد بارگذاری نشده باشد و به درستی طراحی، جابجایی، نصب و روغن کاری شده باشد، خرابی هایی غیر از آنهایی که ناشی از خستگی عناصر غلتشی کلاسیک است، قابل اجتناب هستند. با بهبود تولید بلبرینگ و فرآوری فولاد همراه با تکنولوژی پیشرفته روانکاری، پیشرفت های بالقوه در عمر بلبرینگ می تواند 80 برابر بیشتر از آنچه در اواخر دهه 1950 به دست می آمد یا تا 400 برابر در سال 1940 باشد.
زندگی بلبرینگ پایه
همانطور که قبلا ذکر شد، عمر L10، در میلیونها انقلاب درون نژادی، عمر تئوریکی است که 90 درصد جمعیت بلبرینگ باید بدون شکست در بار عملیاتی خود برابر یا از آن فراتر رود. این بر اساس خستگی عنصر نورد کلاسیک است. عمر پایه یاتاقان که اغلب در کاتالوگ های سازندگان بلبرینگ به آن اشاره می شود، عمر L10 بدون فاکتورهای عمر است که به نوع یاتاقان، فولاد بلبرینگ، پردازش فولاد، عملیات حرارتی، روان کننده و شرایط عملیاتی بستگی دارد.
اکثر یاتاقان ها بر اساس عمر پایه بلبرینگ محاسبه شده با و در مواقعی بدون فاکتورهای عمر انتخاب و اندازه می شوند. هشدار این است که در این زمان محاسبه شده یا قبل از آن، می توان انتظار داشت که 10 درصد از یاتاقان هایی که تحت این بار و سرعت کار می کنند از کار بیفتند. بسیاری از مهندسان متوجه نیستند که عمری که محاسبه کرده اند بر اساس زمانی است که قبل از آن هیچ خرابی رخ نمی دهد، بلکه بر اساس زمانی است که قبل از آن می توان انتظار داشت 10 درصد از یاتاقان ها خراب شوند. این اشتباه می تواند منجر به ادعای ضمانت و مسئولیت محصول برای سازنده تجهیزات شود.
عمر سیستم بلبرینگ
از آنجایی که می توان با اطمینان معقول فرض کرد که هر ماشین دوار دارای دو یا چند یاتاقان است که سیستم را تشکیل می دهد، شما باید علاوه بر عمر بلبرینگ فردی، عمر سیستم بلبرینگ را نیز تعیین کنید. این را می توان با ترکیب زندگی حامل های فردی در یک زندگی واحد برای سیستم به دست آورد.
برای ایجاد عمر سیستم، درک قابلیت اطمینان سری دقیق مورد نیاز است. به یاد داشته باشید که عمر بلبرینگ ها به عنوان یک سیستم همیشه برابر یا کمتر از عمر کوتاه ترین بلبرینگ در سیستم است. به عنوان مثال، فرض کنید یک گیربکس ساده کاهنده سرعت با دو یاتاقان دارید که دنده ورودی را در 3600 دور در دقیقه پشتیبانی می کند و یک دنده خروجی که توسط همان دو نوع یاتاقان با سرعت 900 دور در دقیقه پشتیبانی می شود.
در بار یا گشتاور کامل (100 درصد)، عمر هر یک از یاتاقان های ورودی 2500 ساعت و عمر هر یک از یاتاقان های خروجی 10000 ساعت است. عمر 10 درصدی سیستم 1124 ساعت محاسبه می شود. این بدان معنی است که اگر شما 1000 گیربکس را توزیع می کردید و همه آنها در حداکثر گشتاور به مدت 1124 ساعت کار می کردند، 100 گیربکس حداقل یک بلبرینگ خراب می کردند. سپس این سوال مطرح می شود که چه مدت می توانید گیربکس را در این شرایط بدون نقص کار کنید.
اگر عمر کوتاه ترین یاتاقان در سیستم 2500 ساعت باشد، به طور منطقی می توان انتظار داشت که در 133 ساعت اول کارکرد هر گیربکس هیچ خرابی یاتاقان وجود نداشته باشد. با این حال، گیربکس ها ممکن است همیشه با گشتاور خروجی کامل کار نکنند. فرض کنید گیربکس ها در 50 درصد مواقع با گشتاور کامل، در 30 درصد مواقع یک دوم گشتاور و در 20 درصد مواقع یک چهارم گشتاور کار می کنند. برای محاسبه عمر کل سیستم، باید عمر سیستم L10 را در هر شرایط محاسبه کنید.
با عمر سیستم L10 برابر با 2671 ساعت، 10 درصد از تمام گیربکس های در حال خدمت از نظر تئوری دارای یک یا چند بلبرینگ خراب هستند. اگر مانند مثال قبل، 1000 گیربکس در سرویس دارید و 100 گیربکس خراب دارید، از 4000 بلبرینگ در حال سرویس، 100 بلبرینگ خراب خواهید داشت. به عبارت دیگر، 2.5 درصد از یاتاقان های در حال کار که از کار افتاده اند، 10 درصد از گیربکس های خراب را تشکیل می دهند. 97.5 درصد دیگر از یاتاقان های در حال کار را می توان به طور منطقی فرض کرد که آسیب ندیده و قابل استفاده هستند.
به همین دلیل است که اکثریت قریب به اتفاق یاتاقانهای سالم که از سرویس خارج شدهاند هرگز به عمر L10 محاسبهشده خود نرسیدهاند. بنابراین، بازرسی، کار مجدد و بازگرداندن یاتاقان های سالمی که قبل از رسیدن به عمر L10 حذف شده اند، عملی و مقرون به صرفه است.
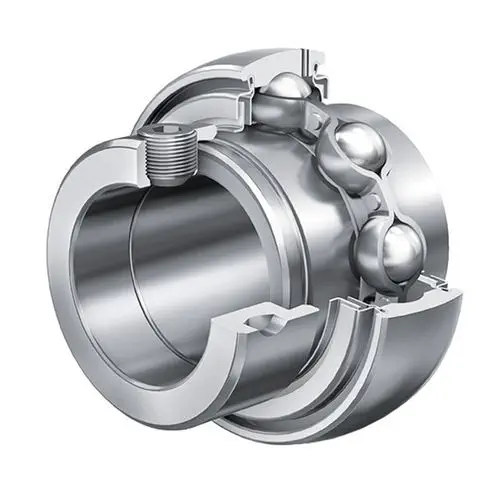
علل حذف بلبرینگ
تا کنون این بحث بر اساس خستگی عنصر غلتشی کلاسیک به عنوان تنها حالت خرابی و حذف بلبرینگ بوده است. با این حال، احتمالاً کمتر از 5 درصد از یاتاقانها به دلیل خستگی عناصر غلتشی، چه منشأ زیرسطحی یا سطحی، از سرویس خارج میشوند.
این علل حذف و خرابی یاتاقان را می توان با طراحی خوب بلبرینگ، نصب صحیح یاتاقان، نگهداری به موقع و روش های خوب روانکاری به حداقل رساند و/یا کاهش داد. با این حال، آنها را نمی توان به طور کامل حذف کرد، که درک و تعیین زندگی حامل را مهم تر می کند.