دلیل از کار افتادن بلبرینگ ها و اقدامات پیشگیرانه از وقوع آن
خرابی بلبرینگ تاثیر زیادی بر صنعت و اقتصاد دارد. هدف از این مقاله بررسی و شناسایی علل عمده ای است که کارایی یاتاقان را محدود می کند و در نتیجه منجر به خرابی یاتاقان می شود. این مطالعه نشان می دهد که علت اصلی خرابی روغن کاری نامناسب عناصر نورد بلبرینگ (تقریباً 80 درصد موارد) و به دنبال آن انتخاب نامناسب بلبرینگ (10 درصد)، نصب نامناسب (5 درصد)، خرابی غیرمستقیم (4 درصد)، و عیوب مواد و خطاهای ساخت (کمتر از 1%).
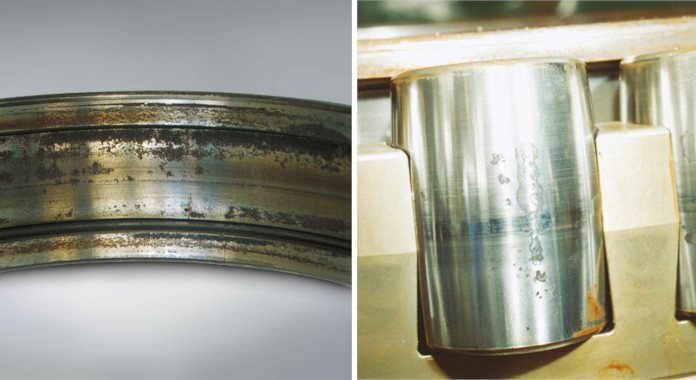
1. روانکاری یاتاقان های غلتشی
یاتاقان نورد یک جزء ماشین آلات است که نقش بسیار مهمی ایفا می کند، زیرا بر عملکرد دستگاه تسلط دارد. اگر یکی از یاتاقان ها خراب شود، نه تنها دستگاه، بلکه خط مونتاژ نیز متوقف می شود و هزینه های استخراج ممکن است بسیار زیاد باشد. به همین دلیل، هر سازنده یاتاقان باید تمام تلاش خود را برای اطمینان از بالاترین کیفیت برای هر یاتاقان و دقیق ترین استفاده و نگهداری از طرف کاربر انجام دهد.
روان کننده ها بین سطوح تماس برای حفظ حرکت مداوم قطعات استفاده می شود. هدف اصلی روانکاری بلبرینگ غلتکی جلوگیری یا کاهش اصطکاک فلز به فلز بین سطوح تماس غلتشی و لغزشی است. این تنها عملکرد روانکاری بلبرینگ نورد نیست. عملکردهای تکمیلی عبارتند از: اتلاف حرارت از یاتاقان، حذف ذرات سایش جامد و آلاینده ها از سطوح تماس نورد، حفاظت در برابر خوردگی، افزایش اثر آب بندی یاتاقان ها.
روغن کاری برای عمر یاتاقان بسیار مهم است. در کاربردهای سنگین، مانند ماشینهای آسیاب نورد، کورهها، اجاقها یا فنهای با دمای بالا، یاتاقانهای نورد ممکن است در معرض دماهای بالاتر از حد معمول قرار گیرند. برای این کاربردها، انتخاب مناسب روانکار و روش روانکاری بسیار مهم است. در کاربردهای صنعتی دو نوع روان کننده مناسب برای استفاده در دمای بالا وجود دارد: گریس و روغن. در موارد خاص، بلبرینگ ها با روان کننده های خشک جامد روانکاری می شوند.
روان کننده گریس برای 90٪ از تمام یاتاقان های نورد استفاده می شود. مقدار گریس مورد استفاده به عوامل زیادی در رابطه با پارامترهای ابعادی و هندسی محفظه، محدودیت های فضا، سرعت کار بلبرینگ و نوع گریس مورد استفاده بستگی دارد. به عنوان یک قاعده کلی، یاتاقان های غلتشی و محفظه آنها باید از 30 تا 60 درصد ظرفیت کل آنها پر شود. اگر سرعت کار و دما افزایش یافت، باید از مقدار کمی گریس استفاده کرد. اگر مقدار گریس بیش از حد باشد، دما افزایش می یابد که ممکن است باعث نرم شدن گریس و نشت موضعی شود. با گذشت زمان گریس خاصیت خود را از دست می دهد و گریس تازه باید در فواصل زمانی مناسب مجدداً عرضه شود. فاصله روغن کاری مجدد به نوع یاتاقان، پارامترهای ابعادی، سرعت کار بلبرینگ و دما بستگی دارد.
در کاربردهای صنعتی، در صورتی که اجزای ماشین مجاور با روغن نیز تامین شوند، یا اگر گرمای تولید شده باید توسط روانکار دفع شود، از روانکاری روغن استفاده می شود. اتلاف گرما در صورتی ضروری است که سرعت چرخش بالا و/یا بارهای زیاد درگیر باشد یا اگر یاتاقان در معرض دماهای بالا باشد. در این مورد، فاصله روغن کاری مجدد به شرایط عملیاتی تحمل (دما، سرعت، بار و غیره)، مقدار روغن و نوع روغن مصرفی بستگی دارد. اگر زمانی که دمای عملیاتی حدود 50 درجه سانتیگراد است از روش روانکاری حمام روغن استفاده می شود، فاصله روغن کاری مجدد باید یک سال باشد. برای شرایط کاری 70 تا 100 درجه سانتیگراد، روغن باید هر سه ماه یکبار تعویض شود. به هر حال، مهم است که سیستم روغن کاری و فرسودگی به طور منظم برای تعیین تعویض روغن بررسی شود.
نوع دیگری از روانکاری بلبرینگ، روانکاری جامد یا خشک است. این روش در کاربردهای صنعتی که در آن یاتاقان های غلتشی تحت بارهای سنگین، حرکات نسبی آهسته و دمای کار بالا قرار می گیرند، استفاده می شود. روانکاری جامد بسیار موثر است و زمان کار نسبتا طولانی را به همراه دارد. رایج ترین روان کننده های جامد مورد استفاده گرافیت و دی سولفید مولیبدن هستند. این روان کننده های جامد به صورت پودر شل، لاک کشویی یا خمیر بر روی سطوح راه آهن اعمال می شوند. روان کننده های گرافیت و دی سولفید مولیبدن را می توان برای دماهای بالای عملیاتی تا 450 درجه سانتی گراد استفاده کرد.

2. شایع ترین علل خرابی بلبرینگ
در عمل، آسیب یا خرابی یک یاتاقان اغلب نتیجه چندین مکانیسم کار به طور همزمان است. خرابی می تواند ناشی از مونتاژ یا نگهداری نامناسب یا در نتیجه ساخت معیوب بلبرینگ یا قطعات مجاور آن باشد.
در برخی موارد، شکست به دلیل سازش در طراحی به نفع اقتصاد یا شرایط عملیاتی پیشبینی نشده است. این ترکیب پیچیده ای از طراحی، ساخت، مونتاژ، بهره برداری و نگهداری است که اغلب در تعیین علت اصلی خرابی مشکل ایجاد می کند. در نظر گرفتن هر ویژگی برای تعیین مطمئن علت خرابی یاتاقان مورد نیاز است. از آنجایی که بیش از یک فرآیند ممکن است اثرات مشابهی روی این سطوح ایجاد کند، توصیف ساده ظاهر معمولاً برای تعیین دلیل شکست کافی نیست.
در صورت آسیب زیاد یا خرابی فاجعه بار یاتاقان، شواهد احتمالی از بین می رود و پس از آن تشخیص علت اصلی خرابی غیرممکن خواهد بود. در همه موارد، آگاهی از شرایط عملیاتی واقعی مجموعه و تاریخچه تعمیر و نگهداری از اهمیت بالایی برخوردار است. به طور معمول، علل خرابی بلبرینگ را می توان در پنج گروه و زیر گروه های مختلف طبقه بندی کرد که در شکل 1 نشان داده شده است.
تکامل تحقیقات تریبولوژیک در دهه های اخیر منجر به افزایش قابل توجه دانش جدید در توصیف مکانیسم های شکست شده است. داده های حاصل از این زمینه تحقیقاتی نشان می دهد که روغن کاری نامناسب رایج ترین دلیل ذکر شده برای خرابی بلبرینگ است و تقریباً 80 درصد خرابی ها را به خود اختصاص می دهد. به طور طبیعی، این درصدها ممکن است بسته به شرایط عملیاتی و شیوههای نگهداری از برنامهای به برنامه دیگر متفاوت باشد.
3. روغن کاری نامناسب
انتخاب روان کننده های یاتاقان مناسب بر اساس تصمیم گیری در مورد انتخاب روغن یا گریس و تعیین نوع افزودنی مورد نیاز است. این تصمیم به عواملی مانند بار عملیاتی، سرعت و دما بستگی دارد.
روانکاری یک عامل کلیدی است که می تواند عمر مفید یاتاقان را خراب کند. برخی از تحقیقات در صنعت بلبرینگ بیان کرده اند که روغن کاری نامناسب می تواند حدود 80 درصد از خرابی یاتاقان ها را تشکیل دهد. خرابی می تواند نتیجه روانکاری طولانی مدت بدون تجدید، روانکاری نامناسب و آلودگی روانکاری باشد.
روانکاری بیش از حد طولانی مدت بدون تجدید و روانکاری نامناسب یاتاقان های نورد نشان دهنده درصد زیادی از خرابی های زودرس بلبرینگ است (هر کدام تقریباً 20٪) و در بیشتر موارد می توان از آنها جلوگیری کرد. روان کننده نامناسب روانکاری است که حاوی مواد افزودنی مناسب نباشد، ویسکوزیته مناسبی نداشته باشد یا ممکن است برای استفاده در چنین کاربرد یا محدوده دمایی طراحی نشده باشد.
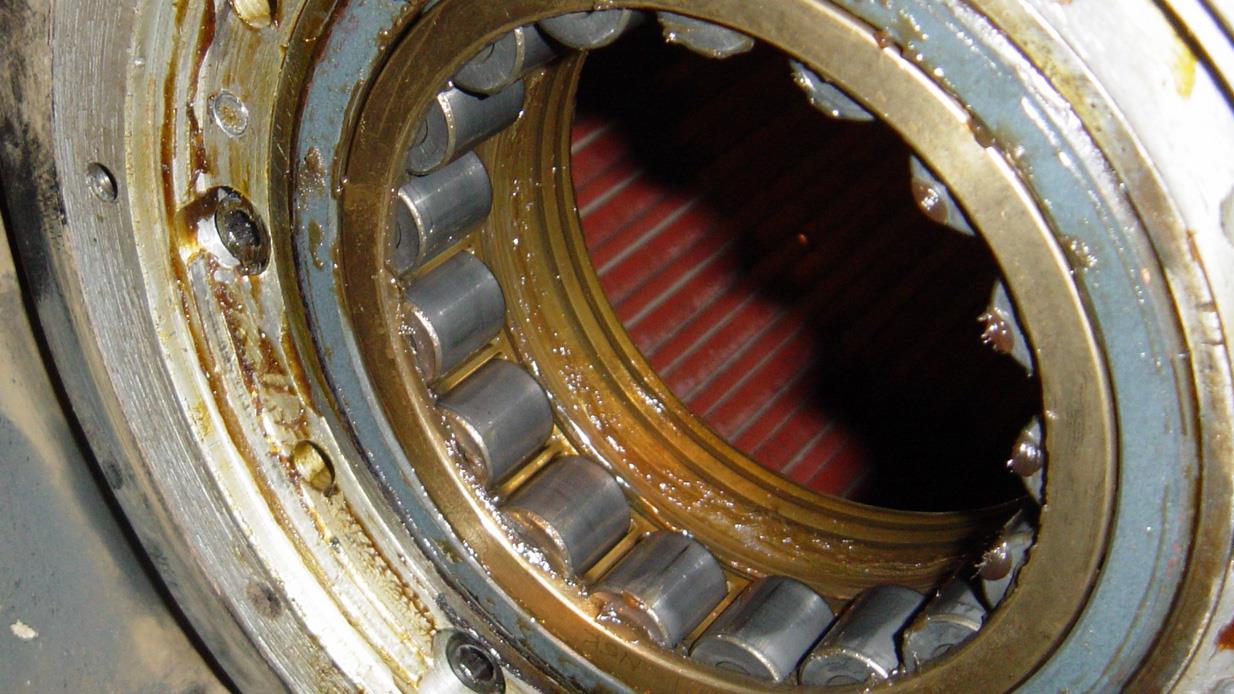
سایش بیرینگ ها می تواند نتیجه روانکاری ناکافی باشد. سطوح تا حدی کدر می شوند که با توجه به درشتی و ماهیت ذرات ساینده متفاوت است. تعداد این ذرات به تدریج افزایش می یابد زیرا مواد از سطوح در حال اجرا و قفس فرسوده می شوند. در نهایت، سایش به یک فرآیند تسریع کننده تبدیل می شود که منجر به از کار افتادن یاتاقان می شود.